Professional Manufacturer Of Hydraulic Metal Cutting Band Saw Machines
Committed to becoming a well-known manufacturer of hydraulic metal cutting band saw machines.

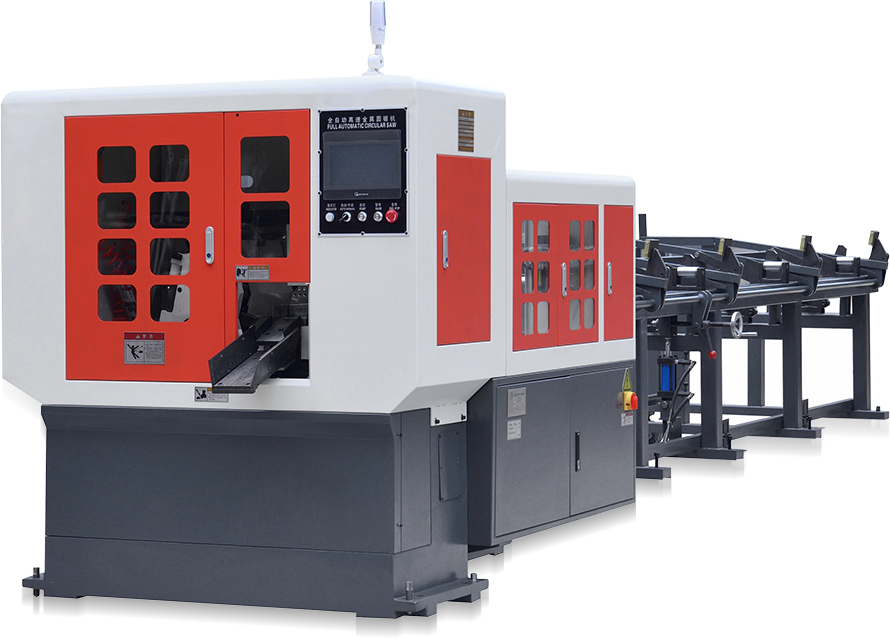
Advanced technical strength and effective technical guarantee.
Flexible business philosophy and professional services.
Advanced manufacturing technology, strictly controlled product quality and good reputation.
For any questions and feedback from customers, we will reply patiently and meticulously.
Pay Attention To Our Latest News And Exhibitions.
The demand for accurate and efficient metal processing has encouraged the use of machines designed for both precision and consistency. Among these, the CNC Full Automatic Metal Band Sawing Machine and the Horizontal Metal Cutting Band Sawing Machine are widely applied in workshops and industrial production. These machines combine automation with reliable cutting performance, making them suitable for different types of metal fabrication. Understanding how they operate helps users select and use the right equipment for their needs. Automated Control System in Action The foundation of a CNC Full Automatic Metal Band Sawing Machine lies in its automated control system. The CNC programming allows users to set cutting parameters in advance, such as dimensions, speed, and feed rate. Once configured, the machine executes the operation without requiring constant manual adjustment. This reduces errors that might occur with traditional manual cutting while also saving time. For facilities that need repetitive cuts with consistent quality, automation ensures a higher level of process control. Precision Cutting Mechanism A defining feature of modern band sawing equipment is the precision cutting mechanism. The blades are designed to run at high speed while being guided by stable structures, ensuring the cut remains accurate. In the case of a Horizontal Metal Cutting Band Sawing Machine, the material is clamped horizontally, allowing even distribution of pressure and improved cutting stability. This setup is useful for handling large sections of metal or long workpieces that require a straight and smooth cut. Speed and Efficiency of Operation Efficiency is often a deciding factor when choosing equipment. The CNC Full Automatic Metal Band Sawing Machine optimizes cutting paths and uses high-speed blades to complete jobs faster. When combined with the horizontal sawing method, the machine supports batch production by maintaining steady throughput. Safety Measures for Operators Safety is a crucial aspect in any cutting operation. These machines are equipped with emergency stop buttons, shields, and protective covers to reduce risks during use. For workshops prioritizing operator safety, these built-in features provide an additional layer of protection without affecting productivity. Durability and Structural Stability Using quality materials in construction ensures the stability of the sawing equipment. The frame and guiding systems are designed to handle vibration and maintain alignment during operation. This stability not only improves the accuracy of each cut but also contributes to longer machine service life. Regular maintenance, such as blade checks and lubrication, further supports consistent performance over time. User-Friendly Operation One of the advantages of adopting modern band sawing machines is their ease of use. Operators do not need extensive technical training to get started. Clear instructions and intuitive control panels allow quick setup and operation. This accessibility enables both experienced workers and new operators to integrate the machine into their workflow without difficulty. Practical Applications in Metal Processing CNC Full Automatic Metal Band Sawing Machines and Horizontal Metal Cutting Band Sawing Machines are applied across industries such as construction, automotive, machinery manufacturing, and metalworking workshops. Their ability to handle different metal types—ranging from steel bars to aluminum profiles—makes them versatile choices. Companies benefit from both precision and efficiency when managing projects that require repetitive or large-volume cutting.By combining automation, precision, safety, and stability, these machines support daily production tasks while meeting the needs of various industries. Understanding how they work helps users make better decisions in selecting equipment that fits their requirements and production scale.
The demand for accurate and efficient metal processing has encouraged the use of machines designed for both precision and consistency. Among these, the CNC Full Automatic Metal Band Sawing Machine and the Horizontal Metal Cutting Band Sawing Machine are widely applied in workshops and industrial production. These machines combine automation with reliable cutting performance, making them suitable for different types of metal fabrication. Understanding how they operate helps users select and use the right equipment for their needs. Automated Control System in Action The foundation of a CNC Full Automatic Metal Band Sawing Machine lies in its automated control system. The CNC programming allows users to set cutting parameters in advance, such as dimensions, speed, and feed rate. Once configured, the machine executes the operation without requiring constant manual adjustment. This reduces errors that might occur with traditional manual cutting while also saving time. For facilities that need repetitive cuts with consistent quality, automation ensures a higher level of process control. Precision Cutting Mechanism A defining feature of modern band sawing equipment is the precision cutting mechanism. The blades are designed to run at high speed while being guided by stable structures, ensuring the cut remains accurate. In the case of a Horizontal Metal Cutting Band Sawing Machine, the material is clamped horizontally, allowing even distribution of pressure and improved cutting stability. This setup is useful for handling large sections of metal or long workpieces that require a straight and smooth cut. Speed and Efficiency of Operation Efficiency is often a deciding factor when choosing equipment. The CNC Full Automatic Metal Band Sawing Machine optimizes cutting paths and uses high-speed blades to complete jobs faster. When combined with the horizontal sawing method, the machine supports batch production by maintaining steady throughput. Safety Measures for Operators Safety is a crucial aspect in any cutting operation. These machines are equipped with emergency stop buttons, shields, and protective covers to reduce risks during use. For workshops prioritizing operator safety, these built-in features provide an additional layer of protection without affecting productivity. Durability and Structural Stability Using quality materials in construction ensures the stability of the sawing equipment. The frame and guiding systems are designed to handle vibration and maintain alignment during operation. This stability not only improves the accuracy of each cut but also contributes to longer machine service life. Regular maintenance, such as blade checks and lubrication, further supports consistent performance over time. User-Friendly Operation One of the advantages of adopting modern band sawing machines is their ease of use. Operators do not need extensive technical training to get started. Clear instructions and intuitive control panels allow quick setup and operation. This accessibility enables both experienced workers and new operators to integrate the machine into their workflow without difficulty. Practical Applications in Metal Processing CNC Full Automatic Metal Band Sawing Machines and Horizontal Metal Cutting Band Sawing Machines are applied across industries such as construction, automotive, machinery manufacturing, and metalworking workshops. Their ability to handle different metal types—ranging from steel bars to aluminum profiles—makes them versatile choices. Companies benefit from both precision and efficiency when managing projects that require repetitive or large-volume cutting.By combining automation, precision, safety, and stability, these machines support daily production tasks while meeting the needs of various industries. Understanding how they work helps users make better decisions in selecting equipment that fits their requirements and production scale.
The landscape of industrial metal cutting is increasingly defined by automation and material science advancements. Integrating sophisticated machinery with purpose-engineered cutting tools is central to meeting demands for efficiency and consistency. The combination of CNC full automatic high-speed circular sawing machines and M42 Bi-metal band saw blades represents a focused approach for operations prioritizing sustained productivity, precision, and prolonged tool service life in automated metal fabrication environments. The Engine of Automation: CNC Full Automatic High-Speed Circular Sawing Machines Modern CNC full automatic high-speed circular sawing machines are designed for controlled, high-throughput metal separation. These systems utilize programmable logic controllers (PLCs) and servo-driven mechanisms to orchestrate the entire cutting sequence–encompassing material feeding, precise clamping, the high-speed sawing operation, and automated handling of the finished part. Core functionalities include rapid blade rotation speeds tailored to reduce cycle times across diverse metals, consistent dimensional accuracy maintained through rigid machine frames and advanced motion control systems, and the capability for extended unmanned operation during batch processing. The performance output of these automated systems is intrinsically linked to the cutting tool's characteristics. Material Innovation: The M42 Bi-Metal Band Saw Blade Advantage The M42 Bi-metal band saw blade exemplifies a specific category of cutting tool developed for rigorous applications. Its construction involves an electron-beam weld joining a high-speed steel (HSS) tooth strip, specifically an alloy containing 8% cobalt (designated M42 grade), to a resilient, high-tensile strength alloy steel backing. This bi-metal design aims to merge critical properties: a tooth material known for its resistance to abrasion and heat deformation encountered during demanding, high-speed cutting operations–particularly beneficial for harder alloys and extended production runs–coupled with a backing material engineered for fatigue resistance and operational stability on circular sawing equipment. The M42 cobalt HSS tooth edge is associated with prolonged edge retention under challenging cutting conditions relative to standard HSS grades. Synergy in Operation: Machine and Blade Integration The practical effectiveness of a CNC full automatic high-speed circular sawing machine is substantially influenced by pairing it with a compatible M42 Bi-metal band saw blade. This strategic combination targets specific operational benefits: Sustained Cutting Performance: The heat and wear resistance inherent in the M42 tooth material supports the maintenance of high cutting speeds over extended durations, aligning with the machine's automation capabilities for continuous operation. Reduced Blade Change Frequency: The potential for prolonged blade service life directly impacts overall equipment effectiveness (OEE) by decreasing downtime associated with blade replacement and subsequent setup adjustments. Consistent Output Quality: The stability provided by the blade's backing material, combined with the machine's precision guidance system, contributes to uniform cut squareness and surface finish consistency throughout production batches. Adaptability Across Materials: This pairing demonstrates capability in processing various metals, including carbon steels, alloy steels, stainless steels, aluminum, and other non-ferrous materials, contingent upon selecting the correct blade pitch and tooth geometry for the specific material profile and cross-section. Optimizing Parameters: Feed, Speed, and Cooling Strategies Achieving the intended performance and longevity from CNC full automatic high-speed circular sawing machines equipped with M42 Bi-metal band saw blades necessitates careful attention to application parameters. Key considerations involve determining the appropriate blade surface speed(measured in SFPM or M/min) for the specific metal alloy being processed, selecting an appropriate feed rate that balances cutting speed with controlled tooth loading and manageable heat generation, and implementing an effective coolant application strategy to dissipate heat, lubricate the cut zone, and efficiently evacuate metal chips. Modern CNC saws typically feature programmable control over these critical parameters, enabling storage of optimized settings for specific jobs. Technical guidance often provides baseline recommendations based on material properties and dimensions. Manufacturing Precision for Predictable Performance Producing components like M42 Bi-metal band saw blades demands specialized metallurgical expertise and rigorous quality control. Essential manufacturing stages include precise electron-beam welding to ensure a robust bond between the HSS tooth material and the alloy backing, controlled tooth grinding processes to achieve exact geometry and sharpness, and specialized heat treatment cycles to develop the required hardness and toughness in the tooth edge. Verification procedures commonly involve destructive and non-destructive testing of weld integrity, hardness testing across the tooth and backing sections, and dimensional inspections for consistent tooth set and pitch. This comprehensive approach aims to deliver blades that meet defined specifications and perform predictably in industrial settings. Research into enhanced machine control algorithms, advanced blade coating technologies, and the integration of sensor data for predictive maintenance represents the ongoing evolution to address emerging material challenges and productivity targets within the fabrication sector, supporting the concept of future-ready manufacturing capabilities.
The landscape of industrial metal cutting is increasingly defined by automation and material science advancements. Integrating sophisticated machinery with purpose-engineered cutting tools is central to meeting demands for efficiency and consistency. The combination of CNC full automatic high-speed circular sawing machines and M42 Bi-metal band saw blades represents a focused approach for operations prioritizing sustained productivity, precision, and prolonged tool service life in automated metal fabrication environments. The Engine of Automation: CNC Full Automatic High-Speed Circular Sawing Machines Modern CNC full automatic high-speed circular sawing machines are designed for controlled, high-throughput metal separation. These systems utilize programmable logic controllers (PLCs) and servo-driven mechanisms to orchestrate the entire cutting sequence–encompassing material feeding, precise clamping, the high-speed sawing operation, and automated handling of the finished part. Core functionalities include rapid blade rotation speeds tailored to reduce cycle times across diverse metals, consistent dimensional accuracy maintained through rigid machine frames and advanced motion control systems, and the capability for extended unmanned operation during batch processing. The performance output of these automated systems is intrinsically linked to the cutting tool's characteristics. Material Innovation: The M42 Bi-Metal Band Saw Blade Advantage The M42 Bi-metal band saw blade exemplifies a specific category of cutting tool developed for rigorous applications. Its construction involves an electron-beam weld joining a high-speed steel (HSS) tooth strip, specifically an alloy containing 8% cobalt (designated M42 grade), to a resilient, high-tensile strength alloy steel backing. This bi-metal design aims to merge critical properties: a tooth material known for its resistance to abrasion and heat deformation encountered during demanding, high-speed cutting operations–particularly beneficial for harder alloys and extended production runs–coupled with a backing material engineered for fatigue resistance and operational stability on circular sawing equipment. The M42 cobalt HSS tooth edge is associated with prolonged edge retention under challenging cutting conditions relative to standard HSS grades. Synergy in Operation: Machine and Blade Integration The practical effectiveness of a CNC full automatic high-speed circular sawing machine is substantially influenced by pairing it with a compatible M42 Bi-metal band saw blade. This strategic combination targets specific operational benefits: Sustained Cutting Performance: The heat and wear resistance inherent in the M42 tooth material supports the maintenance of high cutting speeds over extended durations, aligning with the machine's automation capabilities for continuous operation. Reduced Blade Change Frequency: The potential for prolonged blade service life directly impacts overall equipment effectiveness (OEE) by decreasing downtime associated with blade replacement and subsequent setup adjustments. Consistent Output Quality: The stability provided by the blade's backing material, combined with the machine's precision guidance system, contributes to uniform cut squareness and surface finish consistency throughout production batches. Adaptability Across Materials: This pairing demonstrates capability in processing various metals, including carbon steels, alloy steels, stainless steels, aluminum, and other non-ferrous materials, contingent upon selecting the correct blade pitch and tooth geometry for the specific material profile and cross-section. Optimizing Parameters: Feed, Speed, and Cooling Strategies Achieving the intended performance and longevity from CNC full automatic high-speed circular sawing machines equipped with M42 Bi-metal band saw blades necessitates careful attention to application parameters. Key considerations involve determining the appropriate blade surface speed(measured in SFPM or M/min) for the specific metal alloy being processed, selecting an appropriate feed rate that balances cutting speed with controlled tooth loading and manageable heat generation, and implementing an effective coolant application strategy to dissipate heat, lubricate the cut zone, and efficiently evacuate metal chips. Modern CNC saws typically feature programmable control over these critical parameters, enabling storage of optimized settings for specific jobs. Technical guidance often provides baseline recommendations based on material properties and dimensions. Manufacturing Precision for Predictable Performance Producing components like M42 Bi-metal band saw blades demands specialized metallurgical expertise and rigorous quality control. Essential manufacturing stages include precise electron-beam welding to ensure a robust bond between the HSS tooth material and the alloy backing, controlled tooth grinding processes to achieve exact geometry and sharpness, and specialized heat treatment cycles to develop the required hardness and toughness in the tooth edge. Verification procedures commonly involve destructive and non-destructive testing of weld integrity, hardness testing across the tooth and backing sections, and dimensional inspections for consistent tooth set and pitch. This comprehensive approach aims to deliver blades that meet defined specifications and perform predictably in industrial settings. Research into enhanced machine control algorithms, advanced blade coating technologies, and the integration of sensor data for predictive maintenance represents the ongoing evolution to address emerging material challenges and productivity targets within the fabrication sector, supporting the concept of future-ready manufacturing capabilities.
In metalworking, the performance of cutting tools is defined by how well they meet the demands of modern machinery. CNC full automatic high-speed circular sawing machines, with their rapid operation and precision requirements, place unique pressures on the blades they use. M42 bi-metal band saw blades, engineered for strength and resilience, have emerged as a key solution to these demands, bridging the gap between high-speed automation and consistent cutting results. For those producing and using such tools, this synergy reflects a deep understanding of what metalworking requires—durability, precision, and adaptability. The Demands of CNC Full Automatic High-Speed Circular Sawing Machines CNC full automatic high-speed circular sawing machines are designed to push the boundaries of efficiency. Their high-speed operation—with blade rotation often reaching 300 to 1,800 RPM—cuts through metals like carbon steel, stainless steel, and aluminum at rates far beyond manual or semi-automatic saws. This speed, paired with automated feeding and positioning, means blades must withstand constant, rapid contact with hard materials, enduring friction, heat, and mechanical stress. These machines also demand uniformity. Their CNC systems are programmed to deliver consistent cut dimensions, so blades must maintain stable performance over hundreds or thousands of cuts. Variations in blade sharpness or durability can disrupt this consistency. For industries like automotive part manufacturing or construction metalworking, where batch uniformity is critical, such disruptions carry tangible costs. Adaptability is another demand. CNC machines handle diverse materials—from thin-walled tubing to thick solid bars—and blade performance must adjust accordingly. A blade that falters when switching from aluminum to high-strength steel limits the machine’s versatility, undermining its value in shops with varied workloads. M42 Bi-Metal Band Saw Blades: Strength by Design M42 bi-metal band saw blades are crafted to meet these demands through intentional material engineering. Their core strength lies in a dual-layer construction: a high-speed steel (HSS) cutting edge alloyed with 8% cobalt (the "M42" designation) and a flexible alloy steel backing. This combination marries hardness and toughness—traits often at odds in single-material blades. The cobalt-infused cutting edge retains hardness even at high temperatures, a critical feature when paired with high-speed CNC machines. Friction from rapid cutting generates significant heat; standard blades can soften under this stress, dulling quickly. M42 blades resist this softening, maintaining sharpness through extended use. The alloy steel backing adds flexibility, absorbing the vibrations and flexing that occur during high-speed operation, reducing the risk of breakage. This design also enhances longevity. Compared to carbon steel blades, M42 bi-metal blades can complete more cuts before needing replacement—particularly when cutting abrasive materials like cast iron or alloy steel. For example, in a CNC setup cutting 2-inch carbon steel bars, an M42 blade might last through 2,000 cuts, while a standard blade might require replacement after 500-800. This extended lifespan aligns with the high-volume output of CNC machines, reducing interruptions. How M42 Blades Meet the Real Needs of CNC Machine Tools In practice, the use of M42 blades with CNC fully automatic high-speed circular saws offers tangible benefits across a wide range of industries. In automotive parts production, precision cutting of axles or engine mounts is crucial, and M42 blades can meet the 0.1mm tolerances required by CNC programming. Their heat resistance ensures consistent performance even during 8-hour production runs, where blade overheating could cause cut distortion. For architectural metalworking, processing thick steel beams (6-10 inches in diameter) requires a blade that can engage hard materials without slowing down the machine. The coarse tooth geometry of the M42 blade (10-12 TPI for thick materials) effectively clears chips, preventing blockages and slowing or stopping the CNC system. This allows the machine to maintain high feed rates, ensuring projects are completed on time. In low-volume machining shops, where CNC machines switch between different materials—one hour for aluminum, another for stainless steel—M42 blades can accommodate this. Their versatility eliminates the need for frequent blade changes, streamlining workflow. A single M42 blade can handle both materials simply by adjusting the CNC machine's feed rate to match the blade's performance. Practical Tips for Using M42 Blades with CNC Machines For thin metal (0.5–2 inches), finer teeth (14–18 TPI) reduce chipping; for thicker materials (over 2 inches), coarser teeth (10–12 TPI) improve chip evacuation. The CNC machine's tension setting is also crucial—M42 blades perform reliably when tension is constant to prevent slack and uneven wear. Regular maintenance extends the life of the saw blade. Cleaning saw blades with a wire brush after use removes accumulated chips and prevents corrosion. Inspecting saw teeth for cracks or dull edges before each shift can identify problems early and prevent unexpected failures during operation. For CNC machines, calibrating the feed rate to match the material hardness using the machine's pre-set common metalworking programs ensures the saw blade is not overworked.
In metalworking, the performance of cutting tools is defined by how well they meet the demands of modern machinery. CNC full automatic high-speed circular sawing machines, with their rapid operation and precision requirements, place unique pressures on the blades they use. M42 bi-metal band saw blades, engineered for strength and resilience, have emerged as a key solution to these demands, bridging the gap between high-speed automation and consistent cutting results. For those producing and using such tools, this synergy reflects a deep understanding of what metalworking requires—durability, precision, and adaptability. The Demands of CNC Full Automatic High-Speed Circular Sawing Machines CNC full automatic high-speed circular sawing machines are designed to push the boundaries of efficiency. Their high-speed operation—with blade rotation often reaching 300 to 1,800 RPM—cuts through metals like carbon steel, stainless steel, and aluminum at rates far beyond manual or semi-automatic saws. This speed, paired with automated feeding and positioning, means blades must withstand constant, rapid contact with hard materials, enduring friction, heat, and mechanical stress. These machines also demand uniformity. Their CNC systems are programmed to deliver consistent cut dimensions, so blades must maintain stable performance over hundreds or thousands of cuts. Variations in blade sharpness or durability can disrupt this consistency. For industries like automotive part manufacturing or construction metalworking, where batch uniformity is critical, such disruptions carry tangible costs. Adaptability is another demand. CNC machines handle diverse materials—from thin-walled tubing to thick solid bars—and blade performance must adjust accordingly. A blade that falters when switching from aluminum to high-strength steel limits the machine’s versatility, undermining its value in shops with varied workloads. M42 Bi-Metal Band Saw Blades: Strength by Design M42 bi-metal band saw blades are crafted to meet these demands through intentional material engineering. Their core strength lies in a dual-layer construction: a high-speed steel (HSS) cutting edge alloyed with 8% cobalt (the "M42" designation) and a flexible alloy steel backing. This combination marries hardness and toughness—traits often at odds in single-material blades. The cobalt-infused cutting edge retains hardness even at high temperatures, a critical feature when paired with high-speed CNC machines. Friction from rapid cutting generates significant heat; standard blades can soften under this stress, dulling quickly. M42 blades resist this softening, maintaining sharpness through extended use. The alloy steel backing adds flexibility, absorbing the vibrations and flexing that occur during high-speed operation, reducing the risk of breakage. This design also enhances longevity. Compared to carbon steel blades, M42 bi-metal blades can complete more cuts before needing replacement—particularly when cutting abrasive materials like cast iron or alloy steel. For example, in a CNC setup cutting 2-inch carbon steel bars, an M42 blade might last through 2,000 cuts, while a standard blade might require replacement after 500-800. This extended lifespan aligns with the high-volume output of CNC machines, reducing interruptions. How M42 Blades Meet the Real Needs of CNC Machine Tools In practice, the use of M42 blades with CNC fully automatic high-speed circular saws offers tangible benefits across a wide range of industries. In automotive parts production, precision cutting of axles or engine mounts is crucial, and M42 blades can meet the 0.1mm tolerances required by CNC programming. Their heat resistance ensures consistent performance even during 8-hour production runs, where blade overheating could cause cut distortion. For architectural metalworking, processing thick steel beams (6-10 inches in diameter) requires a blade that can engage hard materials without slowing down the machine. The coarse tooth geometry of the M42 blade (10-12 TPI for thick materials) effectively clears chips, preventing blockages and slowing or stopping the CNC system. This allows the machine to maintain high feed rates, ensuring projects are completed on time. In low-volume machining shops, where CNC machines switch between different materials—one hour for aluminum, another for stainless steel—M42 blades can accommodate this. Their versatility eliminates the need for frequent blade changes, streamlining workflow. A single M42 blade can handle both materials simply by adjusting the CNC machine's feed rate to match the blade's performance. Practical Tips for Using M42 Blades with CNC Machines For thin metal (0.5–2 inches), finer teeth (14–18 TPI) reduce chipping; for thicker materials (over 2 inches), coarser teeth (10–12 TPI) improve chip evacuation. The CNC machine's tension setting is also crucial—M42 blades perform reliably when tension is constant to prevent slack and uneven wear. Regular maintenance extends the life of the saw blade. Cleaning saw blades with a wire brush after use removes accumulated chips and prevents corrosion. Inspecting saw teeth for cracks or dull edges before each shift can identify problems early and prevent unexpected failures during operation. For CNC machines, calibrating the feed rate to match the material hardness using the machine's pre-set common metalworking programs ensures the saw blade is not overworked.
Advancements in automated metal processing continue to shape industrial manufacturing efficiency. Central to this progress is the integration of specialized equipment and purpose-engineered consumables. The combination of CNC full automatic high-speed circular sawing machines and M42 Bi-metal band saw blades represents a targeted approach for operations seeking consistent, rapid metal cutting across diverse materials and profiles. This pairing addresses specific demands for speed, precision, and sustained blade performance in automated production environments. Precision Automation: The Role of CNC Full Automatic High-Speed Circular Sawing Machines Modern CNC full automatic high-speed circular sawing machines are engineered for controlled, efficient metal separation. These systems incorporate programmable logic controllers (PLCs) and servo-driven mechanisms to manage the entire cutting sequence – from material feeding and clamping through the sawing operation itself to finished part handling. Key operational characteristics include rapid blade rotation speeds optimized for reducing cutting cycle times on ferrous and non-ferrous metals, consistent dimensional accuracy maintained through rigid machine construction and precise motion control, and sequences enabling unmanned operation during batch production runs. The effectiveness of these machines is inherently linked to the performance characteristics of the saw blade employed. Material Science in Action: Understanding M42 Bi-Metal Band Saw Blades The M42 Bi-metal band saw blade represents a specific category of cutting tool designed for demanding applications. Its construction involves a high-speed steel (HSS) tooth edge, typically composed of an alloy containing 8% cobalt (M42 grade), electron-beam welded to a flexible, high-tensile strength alloy steel backer. This bi-metal design aims to combine distinct properties: a tooth material offering enhanced resistance to abrasion and heat generated during high-speed cutting, particularly beneficial for harder alloys and long-duration operations, and a backing material providing the necessary fatigue resistance and flexibility for stable operation on circular sawing equipment. The M42 cobalt HSS tooth edge is associated with prolonged edge retention under challenging cutting conditions compared to standard HSS grades. Synergistic Performance: Machine and Blade Integration Selecting the right M42 bi-metal band saw blade significantly impacts the practical value of your CNC fully automatic high-speed circular saw machine. This integration aims to achieve the following: Stable Cutting Speed: The heat and wear resistance of the M42 tooth material enables high cutting speeds to be maintained over time, complementing the machine's automated features. Extended Blade Life: Reduced blade replacement frequency and machine downtime due to blade changes and recalibration improves Overall Equipment Effectiveness (OEE). Consistent Cut Quality: The stability provided by the blade backing material and the machine's rigid guide system helps ensure consistent cut squareness and surface finish from production batch to production batch. Processing Versatility: This combination can be used on a wide range of materials, including carbon steel, alloy steel, stainless steel, aluminum, and non-ferrous metal extrusions, provided the blade pitch and tooth shape are correctly specified based on the material cross-section. Operating Considerations: Feeds, Speeds, and Coolant Achieving the expected performance of a CNC fully automatic high-speed circular saw equipped with an M42 bi-metal band saw blade requires attention to application parameters.Key factors include determining an appropriate blade surface speed (SFPM or M/min) for the specific material being cut; selecting a feed rate that balances cutting speed with tooth load and heat generation; and implementing an effective coolant strategy to control heat, lubricate the cut, and remove chips.Modern CNC saws typically include programmable control of these parameters, allowing optimized settings to be stored in job-specific programs. Technical support typically provides guidance based on material type and size. Application Optimization Technical Support In addition to supplying equipment and saw blades, we frequently provide technical support to help users optimize the use of CNC fully automatic high-speed circular saws and M42 bimetallic band saw blades. This support typically addresses practical application issues: Saw Blade Selection Guide: Recommends appropriate saw blade specifications (pitch, tooth shape, tooth set) based on material type, size, and desired cut quality. Machine Parameter Setup: Provides preliminary recommendations for cutting speed, feed rate, and coolant flow for specific applications. Troubleshooting Assistance: Analyzes cut quality issues (e.g., premature wear, poor surface finish, deviation) and recommends possible adjustments to parameters, blade type, or machine settings. Preventive Maintenance: Provides recommendations on saw blade break-in procedures and routine machine maintenance schedules to ensure stable machine operation and blade life. Safety Procedures: Strengthening standard safety procedures for operating high-speed automated cutting equipment. Focusing on operational efficiency and process stability The focus on CNC fully automated high-speed circular saws paired with M42 bi-metal band saw blades reflects a broader goal within the metalworking industry: improving operational efficiency and ensuring process stability. This combination aims to reduce non-cutting time through automation, lower consumable costs by extending blade life at high speeds, and improve part consistency through programmed precision and stable cutting performance. Continuous evaluation of cutting data and blade consumption patterns informs ongoing process improvements. We continue to explore further developments in machine control systems and blade coating technologies to address the evolving material challenges and productivity targets of the metalworking industry. Integrating sensor data for predictive maintenance is another area of focus, aiming to minimize unplanned interruptions.
Advancements in automated metal processing continue to shape industrial manufacturing efficiency. Central to this progress is the integration of specialized equipment and purpose-engineered consumables. The combination of CNC full automatic high-speed circular sawing machines and M42 Bi-metal band saw blades represents a targeted approach for operations seeking consistent, rapid metal cutting across diverse materials and profiles. This pairing addresses specific demands for speed, precision, and sustained blade performance in automated production environments. Precision Automation: The Role of CNC Full Automatic High-Speed Circular Sawing Machines Modern CNC full automatic high-speed circular sawing machines are engineered for controlled, efficient metal separation. These systems incorporate programmable logic controllers (PLCs) and servo-driven mechanisms to manage the entire cutting sequence – from material feeding and clamping through the sawing operation itself to finished part handling. Key operational characteristics include rapid blade rotation speeds optimized for reducing cutting cycle times on ferrous and non-ferrous metals, consistent dimensional accuracy maintained through rigid machine construction and precise motion control, and sequences enabling unmanned operation during batch production runs. The effectiveness of these machines is inherently linked to the performance characteristics of the saw blade employed. Material Science in Action: Understanding M42 Bi-Metal Band Saw Blades The M42 Bi-metal band saw blade represents a specific category of cutting tool designed for demanding applications. Its construction involves a high-speed steel (HSS) tooth edge, typically composed of an alloy containing 8% cobalt (M42 grade), electron-beam welded to a flexible, high-tensile strength alloy steel backer. This bi-metal design aims to combine distinct properties: a tooth material offering enhanced resistance to abrasion and heat generated during high-speed cutting, particularly beneficial for harder alloys and long-duration operations, and a backing material providing the necessary fatigue resistance and flexibility for stable operation on circular sawing equipment. The M42 cobalt HSS tooth edge is associated with prolonged edge retention under challenging cutting conditions compared to standard HSS grades. Synergistic Performance: Machine and Blade Integration Selecting the right M42 bi-metal band saw blade significantly impacts the practical value of your CNC fully automatic high-speed circular saw machine. This integration aims to achieve the following: Stable Cutting Speed: The heat and wear resistance of the M42 tooth material enables high cutting speeds to be maintained over time, complementing the machine's automated features. Extended Blade Life: Reduced blade replacement frequency and machine downtime due to blade changes and recalibration improves Overall Equipment Effectiveness (OEE). Consistent Cut Quality: The stability provided by the blade backing material and the machine's rigid guide system helps ensure consistent cut squareness and surface finish from production batch to production batch. Processing Versatility: This combination can be used on a wide range of materials, including carbon steel, alloy steel, stainless steel, aluminum, and non-ferrous metal extrusions, provided the blade pitch and tooth shape are correctly specified based on the material cross-section. Operating Considerations: Feeds, Speeds, and Coolant Achieving the expected performance of a CNC fully automatic high-speed circular saw equipped with an M42 bi-metal band saw blade requires attention to application parameters.Key factors include determining an appropriate blade surface speed (SFPM or M/min) for the specific material being cut; selecting a feed rate that balances cutting speed with tooth load and heat generation; and implementing an effective coolant strategy to control heat, lubricate the cut, and remove chips.Modern CNC saws typically include programmable control of these parameters, allowing optimized settings to be stored in job-specific programs. Technical support typically provides guidance based on material type and size. Application Optimization Technical Support In addition to supplying equipment and saw blades, we frequently provide technical support to help users optimize the use of CNC fully automatic high-speed circular saws and M42 bimetallic band saw blades. This support typically addresses practical application issues: Saw Blade Selection Guide: Recommends appropriate saw blade specifications (pitch, tooth shape, tooth set) based on material type, size, and desired cut quality. Machine Parameter Setup: Provides preliminary recommendations for cutting speed, feed rate, and coolant flow for specific applications. Troubleshooting Assistance: Analyzes cut quality issues (e.g., premature wear, poor surface finish, deviation) and recommends possible adjustments to parameters, blade type, or machine settings. Preventive Maintenance: Provides recommendations on saw blade break-in procedures and routine machine maintenance schedules to ensure stable machine operation and blade life. Safety Procedures: Strengthening standard safety procedures for operating high-speed automated cutting equipment. Focusing on operational efficiency and process stability The focus on CNC fully automated high-speed circular saws paired with M42 bi-metal band saw blades reflects a broader goal within the metalworking industry: improving operational efficiency and ensuring process stability. This combination aims to reduce non-cutting time through automation, lower consumable costs by extending blade life at high speeds, and improve part consistency through programmed precision and stable cutting performance. Continuous evaluation of cutting data and blade consumption patterns informs ongoing process improvements. We continue to explore further developments in machine control systems and blade coating technologies to address the evolving material challenges and productivity targets of the metalworking industry. Integrating sensor data for predictive maintenance is another area of focus, aiming to minimize unplanned interruptions.
In metal cutting, where efficiency and precision directly impact productivity, two tools stand out for their ability to balance speed and durability: the CNC full automatic high-speed circular sawing machine and the M42 bi-metal band saw blade. Together, they address the core needs of industries ranging from automotive manufacturing to construction, where consistent, fast cuts on various metals are essential. Backed by expertise in producing reliable cutting equipment, their synergy offers practical solutions for modern metalworking challenges. CNC Full Automatic High-Speed Circular Sawing Machines: Precision in Automation CNC full automatic high-speed circular sawing machines are engineered to streamline metal cutting through automation, reducing manual intervention while boosting speed. Unlike semi-automatic models, these machines integrate computer numerical control (CNC) systems that manage the entire cutting process—from material feeding and positioning to blade activation and cut completion. This automation ensures each cut adheres to programmed dimensions, with errors arising from manual adjustments kept to a minimum. High-speed capabilities are a defining feature. Equipped with powerful motors and optimized blade rotation speeds, they can cut through metals like carbon steel, aluminum, and stainless steel faster than traditional saws. For example, a 2-inch diameter carbon steel rod might take 10-15 seconds to cut with a standard saw, but these machines can complete the same cut in 5-8 seconds, significantly reducing per-piece processing time. Their design also prioritizes adaptability. Many models include adjustable clamping systems to secure different material shapes—round bars, square tubes, or flat sheets—without needing extensive retooling. This flexibility makes them suitable for small-batch production runs and large-scale manufacturing alike, addressing the varied needs of metalworking shops. M42 Bi-Metal Band Saw Blades: Resilience in Every Cut M42 bi-metal band saw blades are crafted to withstand the demands of high-speed cutting, thanks to their unique material composition. They combine a high-speed steel (HSS) edge—alloyed with 8% cobalt, denoted by "M42"—with a flexible alloy steel backing. This dual construction balances hardness and toughness: the cobalt-infused teeth maintain sharpness even when cutting hard metals, while the backing resists fatigue from repeated flexing during operation. Resilience translates to longer blade life. Compared to standard carbon steel blades, M42 bi-metal blades can make 3-5 times more cuts before needing replacement, especially when working with abrasive materials like cast iron or high-strength steel. Their heat resistance is another advantage: the M42 alloy retains hardness at elevated temperatures, preventing premature dulling when friction from high-speed cutting generates heat. Practicality extends to versatility. These blades work with various metal thicknesses, from thin sheets (0.5mm) to thick bars (100mm+), making them a go-to choice for shops handling diverse projects. Their uniform tooth geometry—typically with 10-18 teeth per inch (TPI), depending on material—ensures smooth cuts, reducing the need for post-cut finishing and saving time in production workflows. Working Together: Synergistic Effects in Metal Cutting The true value of the CNC-controlled, fully automatic high-speed circular saw and the M42 bi-metal band saw blade lies in their synergy. The machine's automated features ensure the blade engages the material at the appropriate angle and speed, effectively enhancing cutting efficiency. For example, the CNC system adjusts the feed rate based on material hardness: when machining high-strength steel, the feed rate is reduced to prevent blade overload; when machining aluminum, the feed rate is increased to achieve faster speeds without compromising cut quality. This synergy reduces downtime. The machine's automatic blade tensioning system maintains constant pressure on the M42 blade, preventing slippage or excessive wear that could result in blade breakage. Furthermore, the blade's flexibility means fewer tool changes—critical in high-volume production, where stopping for blade changes reduces productivity. This synergistic approach has proven highly effective in industries such as automotive parts manufacturing, where cutting accuracy (tolerances within 0.1 mm) and speed are paramount. A CNC machine equipped with an M42 insert can produce hundreds of uniformly cut axle components in a single shift, ensuring quality that meets tight deadlines. Similarly, in architectural metalworking, where cutting large steel beams is common, this combination can efficiently handle heavy loads, ensuring projects are completed on time. Practical Tips for Optimal Use Users should select the appropriate insert tooth count (TPI) based on material thickness: when cutting thin metal, choose a finer tooth count (14-18 TPI) to prevent chipping; when cutting thicker metal, choose a coarser tooth count (10-12 TPI) to improve chip evacuation. Regular maintenance is also crucial: cleaning the machine's guide wheels to prevent chip accumulation and inspecting the M42 insert's teeth for damage after cutting abrasive materials can extend the life of both tools. For shops new to CNC automation, starting with preset programs for common materials (available on many machine tool systems) can simplify setup and shorten the learning curve. Parameters can be adjusted incrementally based on specific project needs, allowing users to fine-tune speed and accuracy over time. When it comes to metal cutting, every second counts. The combination of a CNC fully automatic high-speed circular saw and an M42 bi-metal band saw blade offers a balance of speed, precision, and durability, making it an indispensable tool for modern metalworking, supporting efficient, high-quality production across a wide range of industries.
In metal cutting, where efficiency and precision directly impact productivity, two tools stand out for their ability to balance speed and durability: the CNC full automatic high-speed circular sawing machine and the M42 bi-metal band saw blade. Together, they address the core needs of industries ranging from automotive manufacturing to construction, where consistent, fast cuts on various metals are essential. Backed by expertise in producing reliable cutting equipment, their synergy offers practical solutions for modern metalworking challenges. CNC Full Automatic High-Speed Circular Sawing Machines: Precision in Automation CNC full automatic high-speed circular sawing machines are engineered to streamline metal cutting through automation, reducing manual intervention while boosting speed. Unlike semi-automatic models, these machines integrate computer numerical control (CNC) systems that manage the entire cutting process—from material feeding and positioning to blade activation and cut completion. This automation ensures each cut adheres to programmed dimensions, with errors arising from manual adjustments kept to a minimum. High-speed capabilities are a defining feature. Equipped with powerful motors and optimized blade rotation speeds, they can cut through metals like carbon steel, aluminum, and stainless steel faster than traditional saws. For example, a 2-inch diameter carbon steel rod might take 10-15 seconds to cut with a standard saw, but these machines can complete the same cut in 5-8 seconds, significantly reducing per-piece processing time. Their design also prioritizes adaptability. Many models include adjustable clamping systems to secure different material shapes—round bars, square tubes, or flat sheets—without needing extensive retooling. This flexibility makes them suitable for small-batch production runs and large-scale manufacturing alike, addressing the varied needs of metalworking shops. M42 Bi-Metal Band Saw Blades: Resilience in Every Cut M42 bi-metal band saw blades are crafted to withstand the demands of high-speed cutting, thanks to their unique material composition. They combine a high-speed steel (HSS) edge—alloyed with 8% cobalt, denoted by "M42"—with a flexible alloy steel backing. This dual construction balances hardness and toughness: the cobalt-infused teeth maintain sharpness even when cutting hard metals, while the backing resists fatigue from repeated flexing during operation. Resilience translates to longer blade life. Compared to standard carbon steel blades, M42 bi-metal blades can make 3-5 times more cuts before needing replacement, especially when working with abrasive materials like cast iron or high-strength steel. Their heat resistance is another advantage: the M42 alloy retains hardness at elevated temperatures, preventing premature dulling when friction from high-speed cutting generates heat. Practicality extends to versatility. These blades work with various metal thicknesses, from thin sheets (0.5mm) to thick bars (100mm+), making them a go-to choice for shops handling diverse projects. Their uniform tooth geometry—typically with 10-18 teeth per inch (TPI), depending on material—ensures smooth cuts, reducing the need for post-cut finishing and saving time in production workflows. Working Together: Synergistic Effects in Metal Cutting The true value of the CNC-controlled, fully automatic high-speed circular saw and the M42 bi-metal band saw blade lies in their synergy. The machine's automated features ensure the blade engages the material at the appropriate angle and speed, effectively enhancing cutting efficiency. For example, the CNC system adjusts the feed rate based on material hardness: when machining high-strength steel, the feed rate is reduced to prevent blade overload; when machining aluminum, the feed rate is increased to achieve faster speeds without compromising cut quality. This synergy reduces downtime. The machine's automatic blade tensioning system maintains constant pressure on the M42 blade, preventing slippage or excessive wear that could result in blade breakage. Furthermore, the blade's flexibility means fewer tool changes—critical in high-volume production, where stopping for blade changes reduces productivity. This synergistic approach has proven highly effective in industries such as automotive parts manufacturing, where cutting accuracy (tolerances within 0.1 mm) and speed are paramount. A CNC machine equipped with an M42 insert can produce hundreds of uniformly cut axle components in a single shift, ensuring quality that meets tight deadlines. Similarly, in architectural metalworking, where cutting large steel beams is common, this combination can efficiently handle heavy loads, ensuring projects are completed on time. Practical Tips for Optimal Use Users should select the appropriate insert tooth count (TPI) based on material thickness: when cutting thin metal, choose a finer tooth count (14-18 TPI) to prevent chipping; when cutting thicker metal, choose a coarser tooth count (10-12 TPI) to improve chip evacuation. Regular maintenance is also crucial: cleaning the machine's guide wheels to prevent chip accumulation and inspecting the M42 insert's teeth for damage after cutting abrasive materials can extend the life of both tools. For shops new to CNC automation, starting with preset programs for common materials (available on many machine tool systems) can simplify setup and shorten the learning curve. Parameters can be adjusted incrementally based on specific project needs, allowing users to fine-tune speed and accuracy over time. When it comes to metal cutting, every second counts. The combination of a CNC fully automatic high-speed circular saw and an M42 bi-metal band saw blade offers a balance of speed, precision, and durability, making it an indispensable tool for modern metalworking, supporting efficient, high-quality production across a wide range of industries.
Metal fabrication businesses often search for ways to balance precision, speed, and consistent performance across diverse materials. Metal cutting band sawing machines and vertical metal band sawing machines are established solutions that help workshops address these requirements. By understanding how these machines function, how they can be configured, and which practices sustain their effectiveness, operators can enhance daily operations without sacrificing accuracy. Advantages of Vertical Metal Band Sawing Machines Vertical metal band sawing machines differ from horizontal models in both form and use. Their upright design allows operators to guide workpieces manually, which is particularly useful for cutting curves, angles, or irregular profiles. For metal fabrication shops producing custom components, prototypes, or small-batch parts, this flexibility is a significant advantage. The vertical arrangement means the blade moves in a continuous downward motion as the operator pushes the material along the worktable. Operators can quickly reposition pieces and adjust angles without resetting large fixtures. Many vertical machines also feature adjustable blade guides and tilting tables to accommodate more complex geometries. Another benefit involves space utilization. A vertical metal band sawing machine generally has a smaller footprint than horizontal models, freeing up valuable shop floor area. This can make it easier to position the saw near related workstations, such as welding or drilling areas, improving workflow efficiency. Configuring Metal Cutting Band Saws for Your Tasks Metal cutting band sawing machines are available in various capacities and specifications. Selecting the right configuration starts by reviewing the types and sizes of material your operation handles on a regular basis. Machines designed for large cross-sections or heavy billets include wider blade wheels and reinforced frames to support stable cutting over prolonged periods. Blade speed control is another important factor. Different metals and thicknesses require specific cutting speeds to avoid overheating, excessive burr formation, or premature blade wear. Machines with variable speed drives allow operators to fine-tune blade motion, creating smoother cuts and extending tool life. Hydraulic feeding systems, common on larger horizontal models, can also be adapted for vertical band saws to automate repetitive cuts. Shops handling a mix of manual and semi-automated processes may find hybrid configurations practical, especially when managing both custom and standard jobs. Strategies for Maintaining Cutting Consistency Routine checks are fundamental to maintaining performance. Blade tension should be verified before every shift, as incorrect tension can result in blade deflection, wandering cuts, or unexpected breakage. Over time, guide bearings may develop play that affects straightness. Inspecting and replacing these components at defined intervals keeps machines operating predictably. Coolant circulation systems deserve attention as well. Metal cutting generates heat that can damage blades and deform workpieces. Clean coolant reduces friction and washes away chips, preserving surface finish. Operators should monitor coolant levels, clear nozzles, and remove debris from collection trays. Lubrication of moving parts such as the blade wheels, tensioning mechanisms, and feed controls supports smooth motion and reduces wear. Creating a maintenance log with scheduled inspections and part replacements helps avoid unexpected interruptions. Safety Considerations When Operating Vertical Band Saws While vertical metal band sawing machines are user-friendly, they still require consistent attention to safety. Operators should be trained to recognize appropriate feed pressure, as forcing material too quickly into the blade can result in binding or kickback. Personal protective equipment, including eye shields, gloves, and hearing protection, is necessary to limit exposure to metal chips and noise. Work areas should remain clear of loose tools and offcuts that could interfere with handling. Machines should be equipped with emergency stop functions within easy reach. Labels that clearly indicate power switches and blade direction help reduce confusion, particularly when new operators are involved. Integrating Band Saws Into Workshop Layout Optimizing shop layout supports both productivity and safety. Positioning the vertical metal band saw near storage racks or raw material staging areas simplifies handling. When sawing is integrated with downstream processes like milling or welding, strategic placement helps keep materials moving in one direction and reduces manual lifting. For businesses that produce varied batch sizes, modular workstations with mobile tables or conveyors can be helpful. They enable operators to maneuver large or heavy sections into the saw without repositioning the entire machine. In facilities where noise or dust is a concern, partial enclosures or dedicated cutting zones can isolate sawing operations from assembly and finishing work. Clear walkways and defined storage locations for spare blades, coolant supplies, and hand tools further enhance efficiency. Long-Term Value and Performance Considerations Before purchasing a metal cutting band sawing machine or a vertical model, it is wise to evaluate the expected volume and variety of work. A machine that performs steadily at moderate output may be preferable to an oversized unit that demands more maintenance and energy. Assessing available support, spare part accessibility, and training resources can help ensure smoother commissioning and consistent operation over time. Investing in operator training and preventive maintenance contributes directly to predictable cutting results.
Metal fabrication businesses often search for ways to balance precision, speed, and consistent performance across diverse materials. Metal cutting band sawing machines and vertical metal band sawing machines are established solutions that help workshops address these requirements. By understanding how these machines function, how they can be configured, and which practices sustain their effectiveness, operators can enhance daily operations without sacrificing accuracy. Advantages of Vertical Metal Band Sawing Machines Vertical metal band sawing machines differ from horizontal models in both form and use. Their upright design allows operators to guide workpieces manually, which is particularly useful for cutting curves, angles, or irregular profiles. For metal fabrication shops producing custom components, prototypes, or small-batch parts, this flexibility is a significant advantage. The vertical arrangement means the blade moves in a continuous downward motion as the operator pushes the material along the worktable. Operators can quickly reposition pieces and adjust angles without resetting large fixtures. Many vertical machines also feature adjustable blade guides and tilting tables to accommodate more complex geometries. Another benefit involves space utilization. A vertical metal band sawing machine generally has a smaller footprint than horizontal models, freeing up valuable shop floor area. This can make it easier to position the saw near related workstations, such as welding or drilling areas, improving workflow efficiency. Configuring Metal Cutting Band Saws for Your Tasks Metal cutting band sawing machines are available in various capacities and specifications. Selecting the right configuration starts by reviewing the types and sizes of material your operation handles on a regular basis. Machines designed for large cross-sections or heavy billets include wider blade wheels and reinforced frames to support stable cutting over prolonged periods. Blade speed control is another important factor. Different metals and thicknesses require specific cutting speeds to avoid overheating, excessive burr formation, or premature blade wear. Machines with variable speed drives allow operators to fine-tune blade motion, creating smoother cuts and extending tool life. Hydraulic feeding systems, common on larger horizontal models, can also be adapted for vertical band saws to automate repetitive cuts. Shops handling a mix of manual and semi-automated processes may find hybrid configurations practical, especially when managing both custom and standard jobs. Strategies for Maintaining Cutting Consistency Routine checks are fundamental to maintaining performance. Blade tension should be verified before every shift, as incorrect tension can result in blade deflection, wandering cuts, or unexpected breakage. Over time, guide bearings may develop play that affects straightness. Inspecting and replacing these components at defined intervals keeps machines operating predictably. Coolant circulation systems deserve attention as well. Metal cutting generates heat that can damage blades and deform workpieces. Clean coolant reduces friction and washes away chips, preserving surface finish. Operators should monitor coolant levels, clear nozzles, and remove debris from collection trays. Lubrication of moving parts such as the blade wheels, tensioning mechanisms, and feed controls supports smooth motion and reduces wear. Creating a maintenance log with scheduled inspections and part replacements helps avoid unexpected interruptions. Safety Considerations When Operating Vertical Band Saws While vertical metal band sawing machines are user-friendly, they still require consistent attention to safety. Operators should be trained to recognize appropriate feed pressure, as forcing material too quickly into the blade can result in binding or kickback. Personal protective equipment, including eye shields, gloves, and hearing protection, is necessary to limit exposure to metal chips and noise. Work areas should remain clear of loose tools and offcuts that could interfere with handling. Machines should be equipped with emergency stop functions within easy reach. Labels that clearly indicate power switches and blade direction help reduce confusion, particularly when new operators are involved. Integrating Band Saws Into Workshop Layout Optimizing shop layout supports both productivity and safety. Positioning the vertical metal band saw near storage racks or raw material staging areas simplifies handling. When sawing is integrated with downstream processes like milling or welding, strategic placement helps keep materials moving in one direction and reduces manual lifting. For businesses that produce varied batch sizes, modular workstations with mobile tables or conveyors can be helpful. They enable operators to maneuver large or heavy sections into the saw without repositioning the entire machine. In facilities where noise or dust is a concern, partial enclosures or dedicated cutting zones can isolate sawing operations from assembly and finishing work. Clear walkways and defined storage locations for spare blades, coolant supplies, and hand tools further enhance efficiency. Long-Term Value and Performance Considerations Before purchasing a metal cutting band sawing machine or a vertical model, it is wise to evaluate the expected volume and variety of work. A machine that performs steadily at moderate output may be preferable to an oversized unit that demands more maintenance and energy. Assessing available support, spare part accessibility, and training resources can help ensure smoother commissioning and consistent operation over time. Investing in operator training and preventive maintenance contributes directly to predictable cutting results.
Metalworking relies on precise cutting processes, consistent performance, and equipment that can support production volumes that change over time. Metal cutting bandsaws and vertical metal bandsaws remain important tools for shops and fabrication plants that demand consistent results. Understanding how these machines work and what to look for before purchasing can help companies plan projects effectively and achieve reliable results. The Versatile Capabilities of Metal Cutting Bandsaws The metal cutting bandsaw has evolved into a versatile piece of equipment that can process a wide variety of materials, including carbon steel, stainless steel, aluminum, and structural profiles. One of its main advantages is its ability to precisely cut large blocks or bundles of metal stock while reducing waste. This is essential for maintaining predictable material costs and reducing excess scrap. These machines typically feature adjustable blade speeds, allowing the operator to select cutting parameters that are appropriate for a specific material's hardness and cross-sectional size. Speed control not only helps achieve a smoother surface, but also helps extend the life of the saw blade. Depending on the size of the workpiece, horizontal configurations are often used for long gauge materials, while vertical machines are used for contour cutting or finer shapes. Advanced models include hydraulic clamping systems to secure the material during cutting, and automatic material feeding mechanisms that increase efficiency for high-volume production. Understanding these options can help shop managers match machine capabilities to production needs. Vertical Metal Band Saws for Detailed Cutting Vertical metal band sawing machines are valued for their flexibility and relatively compact footprints. Unlike horizontal machines, vertical saws position the blade perpendicular to the table surface, enabling operators to manipulate the material freely while cutting. This configuration is particularly useful for complex shapes, miter cuts, and trimming operations that require visual control. In many fabrication settings, vertical band saws are used to produce templates or prototype parts because they can be guided by hand or with jigs. Blade tension adjustments and table tilt mechanisms further expand the range of possible cuts. When combined with precise guides and calibrated scales, vertical saws can help reduce rework and maintain consistent part dimensions. Before incorporating a vertical saw into the workflow, it is important to consider whether the table size and throat depth align with the dimensions of typical workpieces. Adequate clearance ensures smooth movement and prevents material binding or blade deflection. Considerations for Blade Selection and Maintenance One factor that significantly affects performance is blade choice. Blades are available in a variety of tooth configurations and materials, such as bi-metal and carbide-tipped versions, each suited for particular cutting speeds and metal types. For example, coarse tooth blades clear chips faster on thicker sections, while finer tooth blades are better for thin-walled tubing and precision work. Regular inspection of blades is necessary to detect signs of dullness, chipping, or uneven wear. Operating with worn blades can result in excessive heat generation, rough surfaces, or even unexpected breakage. Keeping spare blades in inventory helps avoid unnecessary downtime during production. In addition to blade care, periodic maintenance of guide bearings, hydraulic systems, and coolant delivery contributes to consistent machine performance. Clear records of maintenance activities allow operators to schedule interventions before problems affect product quality. Safe Operation and Workplace Planning While metal cutting band saws and vertical metal band sawing machines are powerful assets, they must be operated with attention to safety protocols. Proper personal protective equipment, including gloves and eye protection, reduces the risk of injuries from flying chips or accidental contact with moving parts. Positioning machines in well-lit areas with adequate clearance supports safe material handling and inspection. In shared workshop environments, barriers or marked floor zones help separate cutting operations from other activities, lowering the chance of unplanned interference. Clear labeling of control panels and emergency stops simplifies training and improves response time in unexpected situations. When onboarding new operators, providing instruction on correct feed rates, blade tensioning, and coolant use creates a safer, more predictable work environment. Planning for Future Production Requirements Selecting the right metal cutting band sawing machine or vertical band saw requires balancing current production needs with possible growth. Facilities producing occasional batches may prioritize manual feed machines with straightforward controls, while high-volume shops often invest in automated models capable of unattended cutting cycles. Manufacturers may also explore models with programmable settings that store cutting parameters for repeat jobs, reducing setup time between orders. Modular designs or machines with expandable capacity can accommodate evolving requirements without the need for major layout changes. A clear understanding of the intended applications, the types of materials to be processed, and the level of precision required informs better purchasing decisions. Careful planning helps ensure that equipment continues to support productivity without causing unnecessary operating costs.
Metalworking relies on precise cutting processes, consistent performance, and equipment that can support production volumes that change over time. Metal cutting bandsaws and vertical metal bandsaws remain important tools for shops and fabrication plants that demand consistent results. Understanding how these machines work and what to look for before purchasing can help companies plan projects effectively and achieve reliable results. The Versatile Capabilities of Metal Cutting Bandsaws The metal cutting bandsaw has evolved into a versatile piece of equipment that can process a wide variety of materials, including carbon steel, stainless steel, aluminum, and structural profiles. One of its main advantages is its ability to precisely cut large blocks or bundles of metal stock while reducing waste. This is essential for maintaining predictable material costs and reducing excess scrap. These machines typically feature adjustable blade speeds, allowing the operator to select cutting parameters that are appropriate for a specific material's hardness and cross-sectional size. Speed control not only helps achieve a smoother surface, but also helps extend the life of the saw blade. Depending on the size of the workpiece, horizontal configurations are often used for long gauge materials, while vertical machines are used for contour cutting or finer shapes. Advanced models include hydraulic clamping systems to secure the material during cutting, and automatic material feeding mechanisms that increase efficiency for high-volume production. Understanding these options can help shop managers match machine capabilities to production needs. Vertical Metal Band Saws for Detailed Cutting Vertical metal band sawing machines are valued for their flexibility and relatively compact footprints. Unlike horizontal machines, vertical saws position the blade perpendicular to the table surface, enabling operators to manipulate the material freely while cutting. This configuration is particularly useful for complex shapes, miter cuts, and trimming operations that require visual control. In many fabrication settings, vertical band saws are used to produce templates or prototype parts because they can be guided by hand or with jigs. Blade tension adjustments and table tilt mechanisms further expand the range of possible cuts. When combined with precise guides and calibrated scales, vertical saws can help reduce rework and maintain consistent part dimensions. Before incorporating a vertical saw into the workflow, it is important to consider whether the table size and throat depth align with the dimensions of typical workpieces. Adequate clearance ensures smooth movement and prevents material binding or blade deflection. Considerations for Blade Selection and Maintenance One factor that significantly affects performance is blade choice. Blades are available in a variety of tooth configurations and materials, such as bi-metal and carbide-tipped versions, each suited for particular cutting speeds and metal types. For example, coarse tooth blades clear chips faster on thicker sections, while finer tooth blades are better for thin-walled tubing and precision work. Regular inspection of blades is necessary to detect signs of dullness, chipping, or uneven wear. Operating with worn blades can result in excessive heat generation, rough surfaces, or even unexpected breakage. Keeping spare blades in inventory helps avoid unnecessary downtime during production. In addition to blade care, periodic maintenance of guide bearings, hydraulic systems, and coolant delivery contributes to consistent machine performance. Clear records of maintenance activities allow operators to schedule interventions before problems affect product quality. Safe Operation and Workplace Planning While metal cutting band saws and vertical metal band sawing machines are powerful assets, they must be operated with attention to safety protocols. Proper personal protective equipment, including gloves and eye protection, reduces the risk of injuries from flying chips or accidental contact with moving parts. Positioning machines in well-lit areas with adequate clearance supports safe material handling and inspection. In shared workshop environments, barriers or marked floor zones help separate cutting operations from other activities, lowering the chance of unplanned interference. Clear labeling of control panels and emergency stops simplifies training and improves response time in unexpected situations. When onboarding new operators, providing instruction on correct feed rates, blade tensioning, and coolant use creates a safer, more predictable work environment. Planning for Future Production Requirements Selecting the right metal cutting band sawing machine or vertical band saw requires balancing current production needs with possible growth. Facilities producing occasional batches may prioritize manual feed machines with straightforward controls, while high-volume shops often invest in automated models capable of unattended cutting cycles. Manufacturers may also explore models with programmable settings that store cutting parameters for repeat jobs, reducing setup time between orders. Modular designs or machines with expandable capacity can accommodate evolving requirements without the need for major layout changes. A clear understanding of the intended applications, the types of materials to be processed, and the level of precision required informs better purchasing decisions. Careful planning helps ensure that equipment continues to support productivity without causing unnecessary operating costs.
Efficient workshop layout plays a crucial role in improving productivity and safety when working with metal cutting band sawing machines. Vertical metal band sawing machines, with their compact design and versatile cutting capabilities, offer practical advantages for optimizing space and workflow. Understanding how to integrate these machines effectively can help workshops enhance operational efficiency and meet varied metal cutting demands. Space Efficiency and Workshop Organization Vertical metal band saws are designed to take up less floor area compared to some other sawing equipment, making them well-suited for workshops where space is limited. Their vertical orientation allows for easy placement along walls or in corners, freeing up central floor space for material handling or additional machinery. Organizing a workshop with vertical band saws in mind also simplifies the workflow. Materials can be loaded and unloaded without excessive movement, and the clear visibility of the cutting line helps reduce errors. Grouping machines by function or material type further supports a smooth production process. Planning the layout around machine dimensions, including height and operational clearance, ensures safe access for operators and maintenance personnel. Proper positioning of electrical and control panels also contributes to efficient use of space and easier troubleshooting. Flexibility in Metal Cutting Operations Vertical metal band sawing machines offer adaptability to a wide range of cutting tasks. Their ability to adjust cutting angles and speeds allows operators to work with different metals and thicknesses. This versatility means workshops can handle various projects without the need for multiple specialized machines. Incorporating vertical band saws within the workshop layout encourages flexible use of space. The machines can be moved or reconfigured as production needs evolve, supporting diverse workflows from small batch jobs to larger fabrication runs. The vertical design enhances material support and control during cutting, which is particularly beneficial when working with long or heavy stock. This feature improves cut accuracy and reduces waste, important factors in maintaining cost-effectiveness. Safety and Accessibility Considerations Workshop layout must prioritize operator safety when using metal cutting band saws. Vertical band saws provide easier access to the cutting area and controls, helping reduce strain and the risk of accidents. Positioning these machines where operators have clear sightlines and sufficient space to move enhances safety further. In addition to physical space, placing safety equipment like emergency stops, protective guards, and ventilation near the machines is essential. Adequate lighting in the work area helps operators monitor the cutting process and identify potential issues promptly. Maintaining clear pathways around the machines facilitates quick evacuation if needed and allows for efficient material transport. Training personnel on safe operation and layout awareness contributes to a safer workshop environment. Maintenance and Workflow Efficiency Optimizing the layout around vertical metal band saws supports easier maintenance activities. Providing enough clearance for accessing blades, motors, and hydraulic systems reduces downtime and helps keep machines running smoothly. Centralizing related tools and replacement parts near the saws speeds up routine tasks such as blade changes and adjustments. This organization disruptions during production and helps maintain consistent output quality. Aligning workflow paths with machine placement avoids unnecessary handling of heavy materials, reducing labor efforts and potential damage. Efficient material flow from storage to cutting stations contributes to steady productivity. Tailoring Layouts to Workshop Needs Every workshop has unique requirements based on available space, production volume, and types of metals processed. Customizing the placement of vertical metal band sawing machines within these constraints enables better utilization of resources. Consulting with machine suppliers or industry experts can provide valuable insights into layout options that balance space, accessibility, and operational flow. Modular setups or mobile mounting options may be explored for greater flexibility. As production scales or product types change, revisiting the workshop layout ensures that the environment remains conducive to safe and efficient metal cutting activities. Supporting Workshop Success With Thoughtful Design By focusing on space-saving features, operational versatility, safety, and maintenance convenience, integrating vertical metal band sawing machines effectively can enhance workshop performance. A well-considered layout contributes to smoother workflows, reduced downtime, and better resource management.
Efficient workshop layout plays a crucial role in improving productivity and safety when working with metal cutting band sawing machines. Vertical metal band sawing machines, with their compact design and versatile cutting capabilities, offer practical advantages for optimizing space and workflow. Understanding how to integrate these machines effectively can help workshops enhance operational efficiency and meet varied metal cutting demands. Space Efficiency and Workshop Organization Vertical metal band saws are designed to take up less floor area compared to some other sawing equipment, making them well-suited for workshops where space is limited. Their vertical orientation allows for easy placement along walls or in corners, freeing up central floor space for material handling or additional machinery. Organizing a workshop with vertical band saws in mind also simplifies the workflow. Materials can be loaded and unloaded without excessive movement, and the clear visibility of the cutting line helps reduce errors. Grouping machines by function or material type further supports a smooth production process. Planning the layout around machine dimensions, including height and operational clearance, ensures safe access for operators and maintenance personnel. Proper positioning of electrical and control panels also contributes to efficient use of space and easier troubleshooting. Flexibility in Metal Cutting Operations Vertical metal band sawing machines offer adaptability to a wide range of cutting tasks. Their ability to adjust cutting angles and speeds allows operators to work with different metals and thicknesses. This versatility means workshops can handle various projects without the need for multiple specialized machines. Incorporating vertical band saws within the workshop layout encourages flexible use of space. The machines can be moved or reconfigured as production needs evolve, supporting diverse workflows from small batch jobs to larger fabrication runs. The vertical design enhances material support and control during cutting, which is particularly beneficial when working with long or heavy stock. This feature improves cut accuracy and reduces waste, important factors in maintaining cost-effectiveness. Safety and Accessibility Considerations Workshop layout must prioritize operator safety when using metal cutting band saws. Vertical band saws provide easier access to the cutting area and controls, helping reduce strain and the risk of accidents. Positioning these machines where operators have clear sightlines and sufficient space to move enhances safety further. In addition to physical space, placing safety equipment like emergency stops, protective guards, and ventilation near the machines is essential. Adequate lighting in the work area helps operators monitor the cutting process and identify potential issues promptly. Maintaining clear pathways around the machines facilitates quick evacuation if needed and allows for efficient material transport. Training personnel on safe operation and layout awareness contributes to a safer workshop environment. Maintenance and Workflow Efficiency Optimizing the layout around vertical metal band saws supports easier maintenance activities. Providing enough clearance for accessing blades, motors, and hydraulic systems reduces downtime and helps keep machines running smoothly. Centralizing related tools and replacement parts near the saws speeds up routine tasks such as blade changes and adjustments. This organization disruptions during production and helps maintain consistent output quality. Aligning workflow paths with machine placement avoids unnecessary handling of heavy materials, reducing labor efforts and potential damage. Efficient material flow from storage to cutting stations contributes to steady productivity. Tailoring Layouts to Workshop Needs Every workshop has unique requirements based on available space, production volume, and types of metals processed. Customizing the placement of vertical metal band sawing machines within these constraints enables better utilization of resources. Consulting with machine suppliers or industry experts can provide valuable insights into layout options that balance space, accessibility, and operational flow. Modular setups or mobile mounting options may be explored for greater flexibility. As production scales or product types change, revisiting the workshop layout ensures that the environment remains conducive to safe and efficient metal cutting activities. Supporting Workshop Success With Thoughtful Design By focusing on space-saving features, operational versatility, safety, and maintenance convenience, integrating vertical metal band sawing machines effectively can enhance workshop performance. A well-considered layout contributes to smoother workflows, reduced downtime, and better resource management.
Metal Cutting Bandsaw Machines play a vital role in many industrial processes. These machines provide efficient and precise cutting solutions for a variety of metals. Our company specializes in producing metal cutting bandsaw machines and vertical metal bandsaw machines to meet the needs of different customers at home and abroad. Understanding the characteristics and practical applications of these machines can help users choose the right equipment and improve their workflow. Main Features of Metal Cutting Bandsaw Machines Metal cutting bandsaw machines are designed to process various types and thicknesses of metal. Its cutting blade consists of a continuous metal strip with sharp teeth that can smoothly cut through the material. This method reduces waste and provides precise cutting, which is essential for manufacturing and processing. One of the advantages of these machines is their ability to efficiently process large and small workpieces. Adjustable cutting speed and blade tension control allow operators to adjust the performance of the machine according to the material being cut. This flexibility helps reduce saw blade wear and maintain cutting accuracy over time. These machines also focus on safety and user convenience. Features such as automatic shutdown, protective covers, and ergonomic controls reduce the risk of accidents and improve ease of use. Regular maintenance of blades and components ensures consistent performance and extends the life of your machine. Advantages of Vertical Metal Bandsaws Vertical metal bandsaws differ from horizontal models in that their blades are placed vertically, allowing for different cutting styles. This design is particularly useful for cutting longer, heavier metal pieces. The vertical design allows for a more visible cut line, allowing for more precise positioning and calibration. These machines are often equipped with hydraulic or mechanical clamps to firmly clamp the material during the cutting process, reducing vibration and improving cut quality. Vertical bandsaws are widely used in metal fabrication shops, construction sites, and manufacturing plants because of their adaptability and reliability. Adjustability is another important aspect. Operators can easily set cutting angles and speeds to accommodate complex shapes and materials, thereby increasing production efficiency. The vertical placement also saves floor space, making these machines ideal for workshops with limited space. Choose the bandsaw that suits your needs Whether to choose a metal cutting bandsaw or a vertical metal bandsaw depends on the specific job requirements. Horizontal bandsaws are generally suitable for regular straight-line cuts and large-scale production, while vertical bandsaws are better suited for special cuts and irregular shapes. Considering factors such as material type, thickness, production volume, and available workspace can help guide decisions. It is also helpful to evaluate machine features such as blade size compatibility, motor power, and control systems to ensure they align with operational goals. Working closely with suppliers can provide insight into the appropriate machine configuration for each application. Understanding warranty terms, maintenance support, and the availability of replacement parts can help make a wise investment. Maintaining Bandsaws to Ensure Consistent Performance Routine maintenance is essential to maintaining cutting accuracy and machine durability. Regularly checking blade condition, adjusting tension, and lubricating moving parts can help prevent breakdowns. Cleaning debris from the machine and ensuring all safety devices are functioning properly can ensure a safe working environment. Training operators to properly use and maintain machines can reduce errors and extend the life of the equipment. Keeping detailed maintenance logs can help track machine health and schedule timely repairs or part replacements. By following these practices, companies can downtime and maintain a stable production schedule while ensuring consistent product quality. Applications and Industry Use Metal cutting band sawing machines find applications in various industries, including automotive, construction, shipbuilding, and machinery manufacturing. Their ability to handle diverse materials such as steel, aluminum, and brass makes them versatile tools for many fabrication needs. Vertical metal band saws are especially useful when dealing with large structural components, pipes, and profiles. Their precision and adaptability support complex manufacturing processes that demand reliable cutting accuracy. Whether producing parts for mass production or custom fabrication, these machines contribute to efficient workflows and resource savings.
Metal Cutting Bandsaw Machines play a vital role in many industrial processes. These machines provide efficient and precise cutting solutions for a variety of metals. Our company specializes in producing metal cutting bandsaw machines and vertical metal bandsaw machines to meet the needs of different customers at home and abroad. Understanding the characteristics and practical applications of these machines can help users choose the right equipment and improve their workflow. Main Features of Metal Cutting Bandsaw Machines Metal cutting bandsaw machines are designed to process various types and thicknesses of metal. Its cutting blade consists of a continuous metal strip with sharp teeth that can smoothly cut through the material. This method reduces waste and provides precise cutting, which is essential for manufacturing and processing. One of the advantages of these machines is their ability to efficiently process large and small workpieces. Adjustable cutting speed and blade tension control allow operators to adjust the performance of the machine according to the material being cut. This flexibility helps reduce saw blade wear and maintain cutting accuracy over time. These machines also focus on safety and user convenience. Features such as automatic shutdown, protective covers, and ergonomic controls reduce the risk of accidents and improve ease of use. Regular maintenance of blades and components ensures consistent performance and extends the life of your machine. Advantages of Vertical Metal Bandsaws Vertical metal bandsaws differ from horizontal models in that their blades are placed vertically, allowing for different cutting styles. This design is particularly useful for cutting longer, heavier metal pieces. The vertical design allows for a more visible cut line, allowing for more precise positioning and calibration. These machines are often equipped with hydraulic or mechanical clamps to firmly clamp the material during the cutting process, reducing vibration and improving cut quality. Vertical bandsaws are widely used in metal fabrication shops, construction sites, and manufacturing plants because of their adaptability and reliability. Adjustability is another important aspect. Operators can easily set cutting angles and speeds to accommodate complex shapes and materials, thereby increasing production efficiency. The vertical placement also saves floor space, making these machines ideal for workshops with limited space. Choose the bandsaw that suits your needs Whether to choose a metal cutting bandsaw or a vertical metal bandsaw depends on the specific job requirements. Horizontal bandsaws are generally suitable for regular straight-line cuts and large-scale production, while vertical bandsaws are better suited for special cuts and irregular shapes. Considering factors such as material type, thickness, production volume, and available workspace can help guide decisions. It is also helpful to evaluate machine features such as blade size compatibility, motor power, and control systems to ensure they align with operational goals. Working closely with suppliers can provide insight into the appropriate machine configuration for each application. Understanding warranty terms, maintenance support, and the availability of replacement parts can help make a wise investment. Maintaining Bandsaws to Ensure Consistent Performance Routine maintenance is essential to maintaining cutting accuracy and machine durability. Regularly checking blade condition, adjusting tension, and lubricating moving parts can help prevent breakdowns. Cleaning debris from the machine and ensuring all safety devices are functioning properly can ensure a safe working environment. Training operators to properly use and maintain machines can reduce errors and extend the life of the equipment. Keeping detailed maintenance logs can help track machine health and schedule timely repairs or part replacements. By following these practices, companies can downtime and maintain a stable production schedule while ensuring consistent product quality. Applications and Industry Use Metal cutting band sawing machines find applications in various industries, including automotive, construction, shipbuilding, and machinery manufacturing. Their ability to handle diverse materials such as steel, aluminum, and brass makes them versatile tools for many fabrication needs. Vertical metal band saws are especially useful when dealing with large structural components, pipes, and profiles. Their precision and adaptability support complex manufacturing processes that demand reliable cutting accuracy. Whether producing parts for mass production or custom fabrication, these machines contribute to efficient workflows and resource savings.